1. Printing
The printing method is called gravure printing. Different from digital printing, gravure printing needs cylinders for printing. We carve the designs into the cylinders based on different colors, and then use environmental friendly and food grade ink for printing. Cylinder cost depends on bag types, sizes and colors, and it is just a one time cost, next time when you reorder the same design, no more cylinder cost. While normally we will keep the cylinders for 2 years, if after 2 years no reorder, the cylinders will be disposed because of oxidation and storage issues. We now get 5 high-speed printing machines, which can print 10 colors with a speed of 300 meters/min.
If you want to know more about printing, you can check the videos:
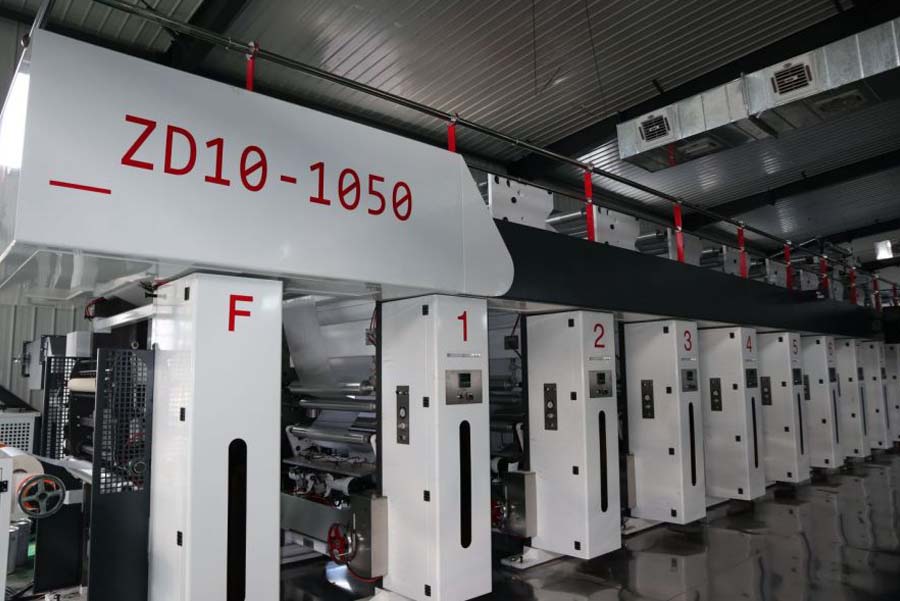
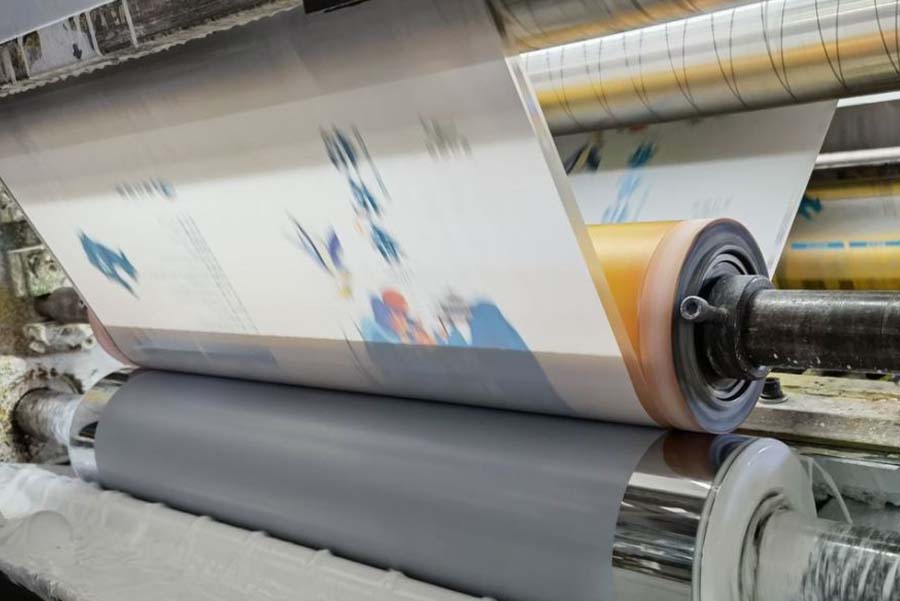
2. Laminating
Flexible bag is also called laminated bag, cos most flexible bag is laminated with 2-4 layers. Lamination is to fulfill the structure of the whole bag, to achieve the functional usage of the bag. Surface layer is for printing, mostly used is matt BOPP, shiny PET, and PA(nylon); middle layer is for some functional use and appearance issue, like AL, VMPET, kraft paper, etc; inner layer makes the whole thickness, and to make the bag to be strong, frozen, vacuum, retort, etc, common material is PE and CPP. After printing on the outside surface layer, we will laminated the middle and inner layer, and then laminated them with outside layer.
If you want to know more about printing, you can check the videos:
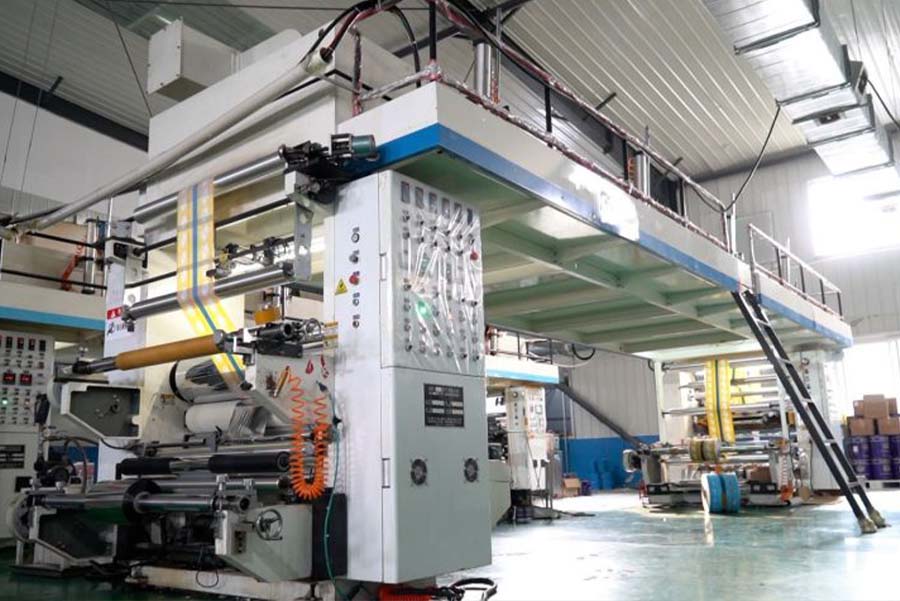
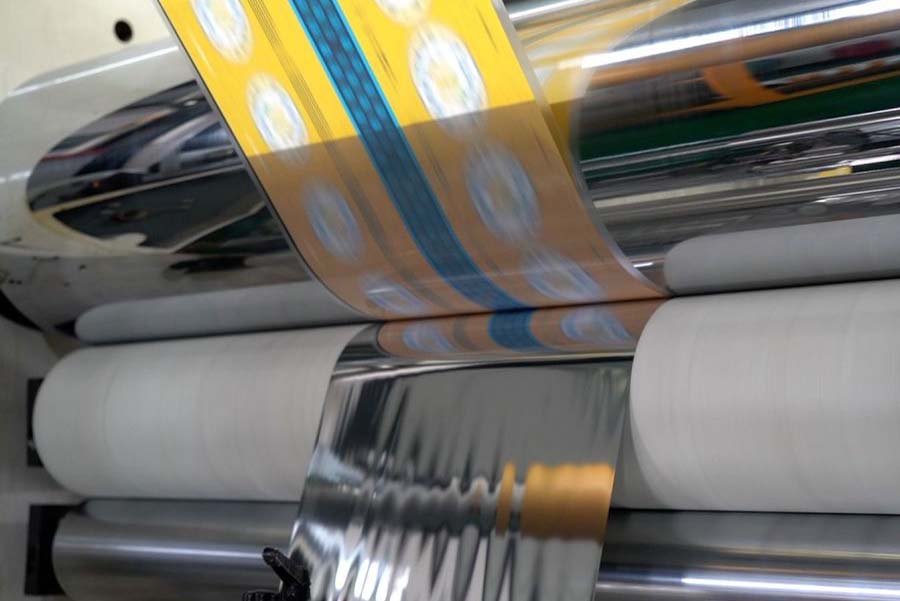
3. Solidifying
Solidifying, is the process of putting the laminated film into the drying room to make the main agent and curing agent of the polyurethane adhesive react and cross-link and interact with the surface of the composite substrate. The main purpose of solidifying is to make the main agent and the curing agent fully react within a certain period of time to achieve the best composite strength; the second is to remove the residual solvent with low boiling point, such as ethyl acetate. Solidifying time is from 24 hours to 72 hours for different materials.
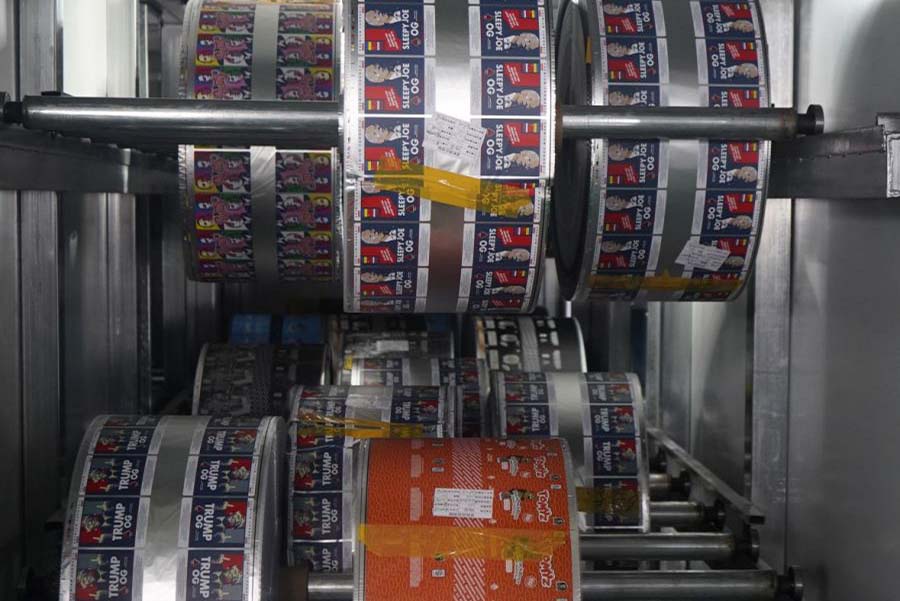
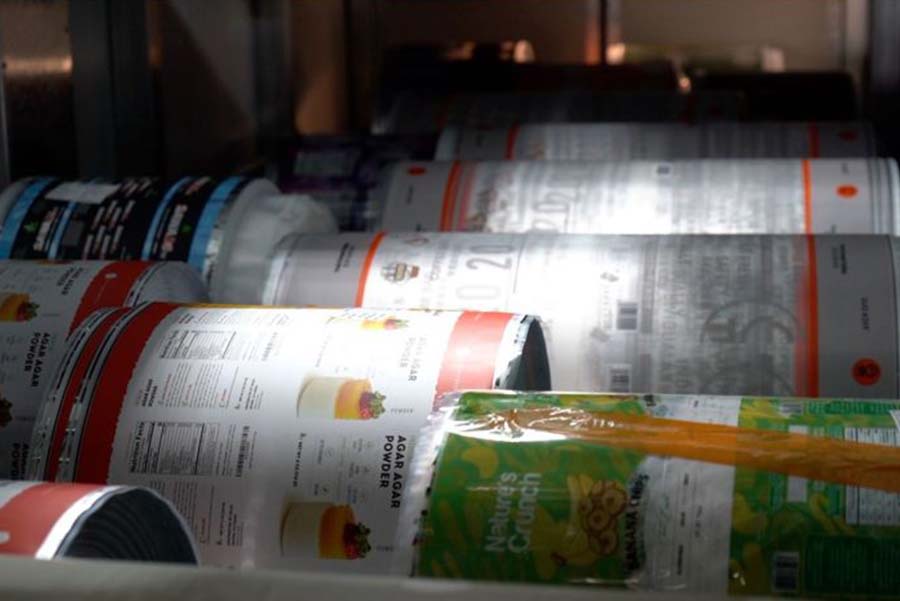
4. Cutting
Cutting is the last step for production, before this step, no matter what kind of bags you ordered, it is with a whole roll. If you order film rolls, then we will just slit them into proper sizes and weights, if you order separate bags, then that is the step we fold and cut them into pieces, and also this is the step we add zipper, hang hole, tear notch, gold stamp, etc. There are different machine according to different bag types-flat bag, stand up bag, side gusset bag and flat bottom bags. Also if you order shaped bags, this is also the step that we use mould to curve them into the right shape you require.
If you want to know more about printing, you can check the videos:
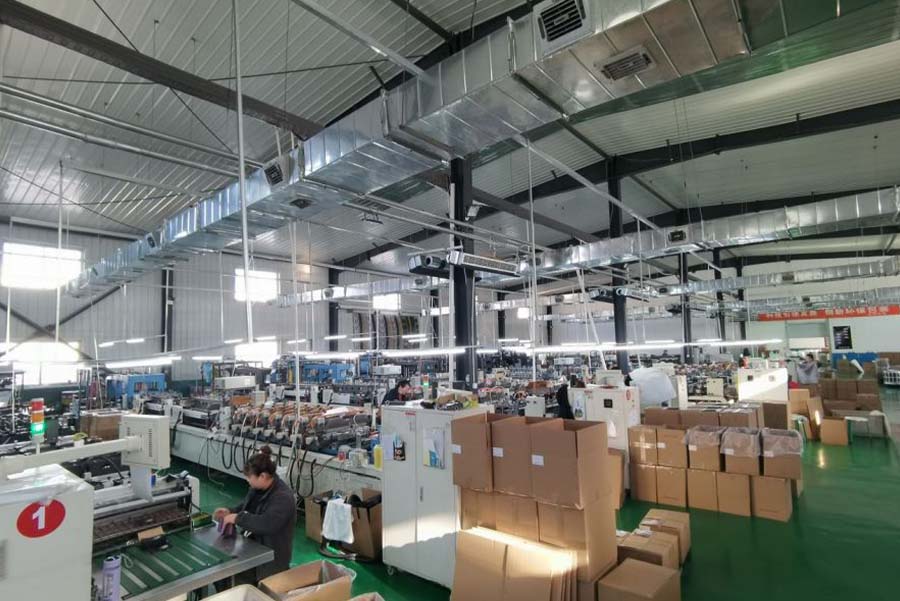
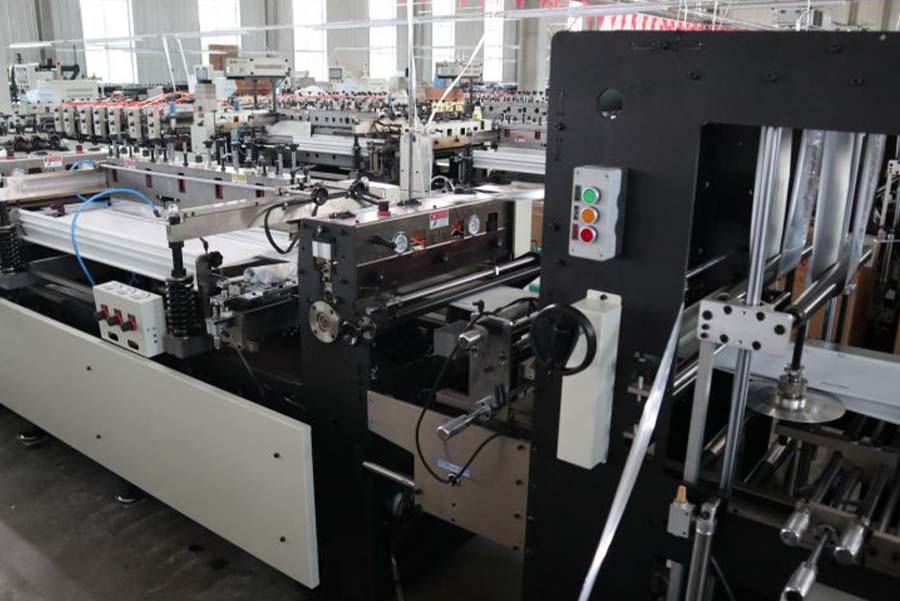
Post time: Jul-14-2022